
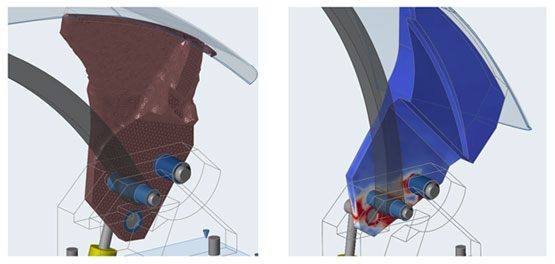

SolidThinking Inspire, SolidThinking Click2Cast, SolidThinking Click2Form, HyperWorks. Optimize for Manufacturability Arrive at the ideal design direction extremely early in the process: topology optimization is based on physics and observes manufacturing process constraints. the results from OptiStruct and Inspire, respectively, in Figur e 5. Department of Mechanical Engineering & Material Science. With solidThinking’s Inspire software, structurally efficient parts are easy to design - saving cost, strengthening durability, and improving safety. Inspire enables both simulation analysts and designers to perform what-if studies faster, easier, and above all earlier, encouraging collaboration and reducing product time to market. In this product review, Architosh looks at the unique solidThinking Inspire 2014 CAE-based industrial design and architecture design tool for optimizing parts and structures for weight and strength. The Material option further opens up a drop-down list from which a material may be selected. Each part is assigned a material by clicking on the Material option in the drop-down menu which appears on right clicking it. For the 2017 release, the product teams employed a tireless focus on both improving current product usability, as well as adding multiple new features that have been requested by customers. Assign Material: In order to correctly analyze the model, its constituent materials should be known. Too many structural components are designed with more weight and material than what’s actually required. The new feature-packed release of the solidThinking Design Suite consisting of solidThinking Inspire 2017 and solidThinking Evolve 2017 is now available. David Anderson of Exact Engineering will share how he redesigned a critical aerospace bracket, reducing weight by an incredible 70%, even while making the part stiffer. Together with solidThinking, a leading provider of design optimization software, we will feature real world customers who have designed radically better products that can only be made via additive manufacturing. Attendees will learn how 3D printing is being used to produce parts that are lighter weight, stronger, better performing and safer. What if you could design the ideal structural part without any constraints, and use the freedom of complexity that metal 3D printing enables to make that part a reality? This webinar will showcase how 3D Systems printers enable better products through mass complexity.
